
OUR INNOVATION,
YOUR SOLUTION

The Sensify Gatekeeper System (SGS) delivers a revolutionary solution giving LPG companies worldwide unparalleled control over their cylinders for the first time, thereby eradicating theft and piracy and ensuring safety and customer loyalty, whilst analysing and optimising operations.
SGS is a world-leading combination of mechanical, electronic, software and radio frequency engineering. It delivers a unique ‘lock and key’ system that secures cylinders with its tamper-proof valve, featuring built-in RFID technology, that can only be unlocked by specialist filling nozzles controlled by a secure cloud-based application.
​
​
SMART, SAFE AND SECURE
​
SGS enables LPG companies to track in realtime the life cycle of their cylinders from global supplier depots, filling sites, distributors and re-sellers. It also enables LPG companies to block the filling of any of its cylinders, wherever they are in the world, therefore rendering them useless if they have been stolen or if a rogue filler attempts to use them. This realtime tracking functionality, allows enforced servicing or removal of cylinders from the market, ensuring the safety and compliance of all of the company’s LPG cylinders.
The SGS Software provides users with recommendations for optimisation and increased performance. Our software is a standalone solution that can be integrated with all ERP and accounting software programs.
Our 'POL' Smart Valve

RFID
Tag
Relief
Valve
Sensify
Smart
Tech
Our 'Compact' Smart Valve

Inlet /
Outlet
Sensify
Smart
Tech
Relief
Valve
RFID
Tag
HOW IT WORKS


Cylinder
ID
Company
ID
Company
Name
Manufacture
Date
Validation
Date
Tare
Weight
Cylinder
Size
Identification
Validation
Compliance
Verification
Cylinders are fitted with revolutionary SGS Valves, which are programmed with required cylinder information.
Once programmed, the information can only be changed by an authorised person within the company using our SGS Software.
Cylinders connected to the filling scales are scanned by an SGS Filling Nozzle to verify the information on the SGS Valves.
The SGS Software will only allow filling of the cylinder once all protocols have been verified.
The SGS Controller is connected to the SGS Database via Wi-Fi, 3G or 4G. In the event of a network failure, the SGS Controller remains operational until connection is re-established.
Information from the cylinder is verified and processed by the SGS Controller.
The SGS Controller can be connected to multiple filling nozzles and is installed and configured to each filling site’s requirements.
If the cylinder does not meet all protocols, the SGS Filling Nozzle will ‘soft-lock’ the cylinder and an error message will be displayed.
The cloud-based SGS Database acts as a secondary verification source, which is used to verify compliance orders such as cylinder recalls. It stores the data of each and every cylinder, filling site, filling transaction and delivery. Cylinder information is sent back to the SGS Controller which then executes the appropriate commands.
Uniquely assigned login web portals allow SGS Software users to view data from operations, build reports and set parameters.
SGS CONTROLLER
SGS DATABASE
FROM FILLING TO DELIVERY

STEP 1
STEP 2
STEP 3
STEP 4
STEP 5
STEP 6
STEP 7
SGS Controller
SGS Filling Nozzle
SGS 'POL' Valve
SGS Cloud Database
Delivery/Collection
Delivery/Collections Scanned

STEP 1:
Cylinders installed with SGS Valves are connected to an SGS Filling Nozzle which reads the built-in tamper-proof RFID tags.
​
STEP 2:
The information is sent to the SGS Controller for verification and access is either granted or denied.
​
STEP 3:
The SGS Controller sends the completed filling transaction to the SGS Cloud Database.
​
STEP 4:
The SGS Cloud Software updates the filled cylinder status and the system confirms to the user that it is ready for dispatch.
​
STEP 5:
The filled cylinder is loaded and delivered to the customer.
STEP 6:
The customer’s details are entered on delivery and the cylinder is scanned. Empty cylinders are scanned and upon return to the filling depot their validation / maintenance record is checked before being approved for refilling.
​
STEP 7:
All data is updated to the SGS Cloud Database in realtime.
FEATURES & BENEFITS

Validation
Control
This takes full control of the cylinder maintenance in order to ensure customers always receive a properly maintained, full cylinder.
​
Validation Control records:
​
-
Exactly who serviced the cylinder
-
When it was last serviced
-
What has been done to the cylinder
​
It also sets enforced validation/maintenance periods by ‘soft locking’ the cylinders when they are due.

Compliance
The SGS Software allows full control for users to set and enforce their filling operations standards, for example:
​
-
The removal of their old cylinders from the market by way of a simple recall order.
-
The recall of faulty cylinders by entering the cylinder details.
-
The ability to set and enforce compliance / maintenance standards across different filling stations.

Access
Control
Through the increase of cylinder circulation rate by securing, tracking, recovering and maintaining cylinders, users can reduce the number of new cylinder purchases thereby increasing profits effortlessly.
​
Users can:
​
-
Prevent rogue fillers and cross filling
-
Prevent the filling of invalidated cylinders

Manage
Cylinder
Rotations
Not only does the SGS Software increase profitability by ensuring an increase in cylinder rotations, it allows the user to manage and monitor cylinder rotation rates to ensure cylinders that are more often filled and used, are regularly inspected and checked for safety.

Customer
Delivery
The SGS Software assigns the cylinder’s ID to the customer, stores the customer’s information and the delivery location. The delivery is then confirmed by the customers signature.

Condition
Monitoring
The SGS Software monitors equipment remotely and provides users with the ability to schedule routine maintenance thereby eliminating downtime and maintaining maximum productivity.

Customer
Value
Monitoring
The SGS Software calculates the value of each customer regionally by monitoring customer usage over a determined period through cylinder deliveries and combines this data with the total regional deliveries to evaluate an areas market value in relation to the volume of LPG consumed.
DASHBOARD & ANALYTICS

DASHBOARD
​
The dashboard has been designed for ease of use which enables users to access detailed information effortlessly by fast navigation showing realtime displays regarding its current operations.
​
​
​
​
THE CLOUD
​
The SGS Software is entirely cloud-based which
provides users with peace of mind and access over multiple devices.
​
​
​
​
MANAGEMENT DASHBOARDS
​
Each filling station is assigned with its own account, unique username and password. Each user dashboard displays only its own performance and information.
The user’s primary filling station’s ‘Management Dashboard’ displays the content of all of its filling stations which enable it to assess each individual site’s performance, customer deliveries, when cylinders are due for validation etc. in order to maximise efficiency and profits.
​
​
​
​
PERFORMANCE INDICATORS
​
Performance indicators are displayed on the Dashboard. Data from current operations are compared to previous periods to calculate whether a company / distributor is underperforming or exceeding previous periods.
Sensify
Smart
Tech


Relief
Valve
RFID
Tag

DEVELOPMENT ROADMAP

Customer
Profiling
The user can view customer consumption patterns in order to establish their LPG usage requirements, demographics and therefore value to the company.

Cylinder Activity
Analysis
The user can view customers’ consumption over designated periods in order to determine regional peak and off-peak consumption patterns.

Forecasting
Accurately forecast when the next scheduled delivery should be and when cylinder shortages will occur.

Average Cylinder
Rotations
View the rotation rate of individual cylinders or the average rotation rate of a combined fleet and the factors that influence cylinder rotations.
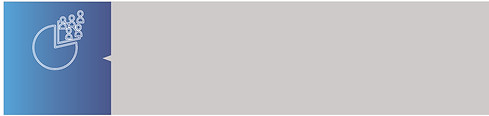
Market
Segmentation
SGS verifies and provides detailed reports on the user’s high volume consumption areas, most active regions, declining regions and customer preferences within the supply chain.
BESPOKE SGS AI SOFTWARE
ADDITIONAL SENSIFY PRODUCTS


Benefits of SGS
Artificial Intelligence
Productivity
Optimisation
PINN
Sales
Application
Inventory
Management System
(IMS)
Sensify
'Cash for Gas' Card
Decision
Making